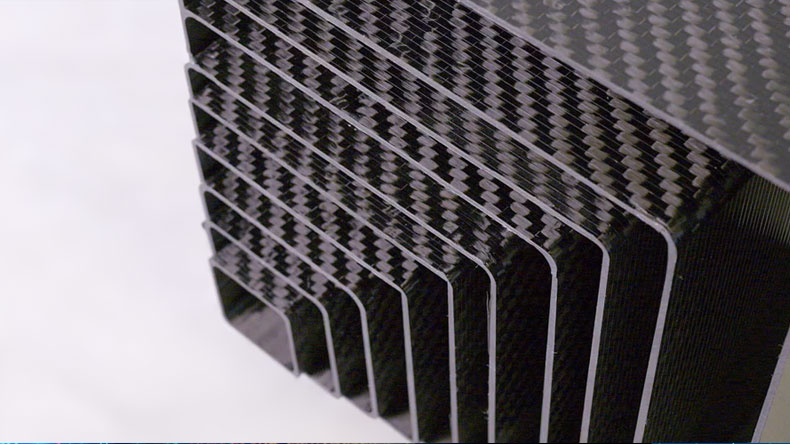
In the race for lighter, stronger, and more efficient materials, one substance has taken center stage: carbon fiber. Once a niche material used primarily in aerospace, carbon fiber is now making waves in automotive, construction, medical, and even consumer electronics.
For business leaders, manufacturing executives, and financial investors, understanding the full potential of carbon fiber is no longer optional—it’s strategic.
Carbon fiber is a high-performance material composed mostly of carbon atoms arranged in a crystalline formation. These fibers are incredibly thin—often thinner than a human hair—but remarkably strong and stiff. When woven together and bonded with resin into a composite, the resulting material is lighter than aluminum yet stronger than steel. This unique combination of properties makes carbon fiber indispensable for industries aiming to reduce weight without compromising strength.
The manufacturing of carbon fiber is a complex, multi-stage process:
● Precursor Production: The process begins with a precursor material, most commonly polyacrylonitrile (PAN), though rayon or pitch may also be used.
● Stabilization: The PAN fibers are heated in air at around 200–300°C to chemically alter their bonding structure.
● Carbonization: These stabilized fibers are then exposed to very high temperatures—often up to 2,000°C—in an oxygen-free environment to drive off non-carbon elements, leaving behind tightly bonded carbon atoms.
● Surface Treatment and Sizing: The fibers are treated to improve bonding with resins and then coated with protective sizing.
● Weaving and Laminating: Fibers are woven into fabrics or arranged in unidirectional layers and impregnated with resin to form carbon fiber sheets, carbon fiber wraps, and other customized components.
The high cost of this process—primarily due to energy consumption and long production cycles—is one reason carbon fiber remains a premium material. However, advancements in automation and recycling are steadily driving costs down.
In today’s fast-evolving industrial landscape, carbon fiber has transitioned from a specialty aerospace material to a high-demand strategic commodity. With its applications expanding into electric vehicles, wind energy, medical devices, and consumer electronics (e.g., carbon fiber phone case, carbon fiber insoles), the financial upside is significant—both for investors and manufacturers.
As of 2024, the global carbon fiber market is valued at approximately USD 5.39 billion, with projections pointing to USD 11.06 billion by 2032, reflecting a compound annual growth rate (CAGR) of 9.4%. Some analysts forecast even steeper growth, estimating up to USD 13.7 billion by 2034. The expansion is largely driven by rising demand in lightweight structural composites, particularly in automotive and aerospace sectors.
Aerospace applications account for 30%+ of carbon fiber consumption, especially in aircraft frames and interiors.
The automotive sector follows closely at 22%, focusing on performance upgrades such as carbon fiber hood and interior panels for weight reduction and energy efficiency.
New applications in construction reinforcement (e.g., carbon fiber wrap for seismic retrofitting) and smart wearables using carbon fiber strain sensors further broaden market potential.
Toray Industries, the world’s largest carbon fiber producer, reported over ¥300 billion (~USD 2.1 billion) in carbon fiber composites revenue for FY2024–2025, marking a 3% year-over-year increase. Global production capacity from major suppliers is projected to reach 71,000 metric tons in 2025, up from 64,000 in 2024.
Hexcel Corporation, a U.S.-based composite leader, reported USD 474 million in Q4 2024 revenue, driven by double-digit growth in aerospace composites. Its free cash flow surpassed USD 200 million, reinforcing investor confidence in the sector’s long-term value.
Despite strong growth, the sector faces notable challenges:
● Production costs remain high due to energy-intensive manufacturing and reliance on PAN precursors.
● Recyclability and sustainability are still evolving; end-of-life strategies for carbon fiber sheets and molded parts remain limited.
● Price competition from advanced aluminum alloys and hybrid composites may pressure margins.
However, as carbon fiber becomes central to clean technology and structural innovation, its value as a long-term industrial investment remains robust.
The automotive industry has aggressively adopted carbon fiber to meet fuel-efficiency and performance demands. From the lightweight carbon fiber hood in sports cars to entire monocoque structures in EVs, the material improves acceleration, braking, and fuel economy. Tesla, BMW, and Lamborghini all utilize carbon fiber extensively. According to MarketsandMarkets, the global carbon fiber market is expected to grow from $4.7 billion in 2023 to $8.9 billion by 2028, driven largely by automotive and aerospace adoption.
In construction, carbon fiber wrap is used to reinforce aging concrete structures such as bridges and columns. These wraps help manage carbon fiber strain under load, allowing engineers to retrofit buildings without costly demolition. Compared to steel reinforcement, carbon fiber composites are corrosion-resistant and require less maintenance—ideal for long-term asset performance.
Carbon fiber insoles, braces, and prosthetic limbs are revolutionizing orthotics with lightweight, ergonomic solutions. Hospitals and clinics value the material for its biocompatibility, rigidity, and durability. This application also intersects with rising healthcare investments in assistive technology, especially in aging societies.
Beyond industry, carbon fiber has entered the consumer space. The carbon fiber phone case is a status symbol among tech enthusiasts—lightweight, durable, and sleek. From premium luggage to sporting goods, consumer-grade composites are a growing segment of the market, especially as manufacturing scales and costs decline.
As demand for high-performance materials grows across multiple sectors, carbon fiber is proving itself as a defining material of the 21st century. Its balance of strength, stiffness, and weight positions it as a solution to modern manufacturing and infrastructure challenges. For business owners, investors, and engineers alike, understanding carbon fiber’s capabilities—whether in carbon fiber strain resistance or consumer applications like carbon fiber insoles—is not just technical knowledge, but a competitive advantage.