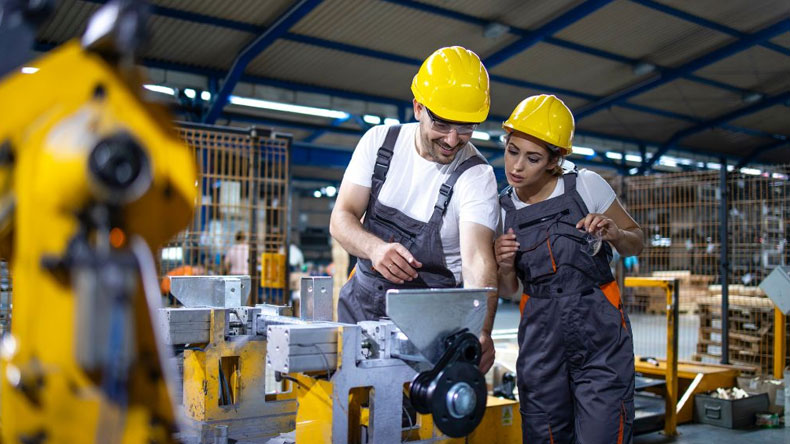
In today’s fast-paced and precision-driven manufacturing landscape, tooling is no longer a mere support function—it is a strategic differentiator. Cutting-edge tooling techniques, encompassing advanced materials, smart sensor integration, and data-driven optimization, are empowering enterprises to enhance productivity, ensure consistency, and reduce waste. As global competition intensifies and tolerance for inefficiencies drops, the role of modern tooling in business operations has become increasingly central.
Advanced tooling techniques serve far more than the basic purpose of material removal. In a modern enterprise, tooling affects every layer of value creation:
● Production Efficiency: High-performance tools reduce cycle times, minimize downtime, and optimize resource use.
● Product Quality: Precision tooling enables tighter tolerances, better surface finishes, and more consistent results.
● Operational Agility: Modular and reconfigurable tooling supports fast changeovers and flexible manufacturing lines.
● Cost Management: Improved tool life and machining efficiency directly reduce per-part production costs.
By integrating cutting-edge tooling into their operations, enterprises can unlock these benefits and establish a scalable, responsive, and future-ready production model.
Modern manufacturing demands high precision, speed, and adaptability—all of which rely on advances in tooling technology. Below are some of the most transformative tooling techniques currently reshaping how enterprises approach production. Each not only addresses performance but also contributes to sustainability, digital integration, and cost-effectiveness.
High-Speed Machining involves using lightweight tools, higher spindle speeds, and optimized tool paths to cut materials at significantly faster rates than traditional methods.
Application: Ideal for aluminum, composites, and certain steel grades in aerospace, mold-making, and automotive parts.
Advantages: Reduces machining time by up to 50%, improves surface finish, and decreases tool wear due to lower cutting forces.
Enterprise Impact: Enables rapid prototyping and low-volume high-precision runs without compromising quality.
This technique uses liquefied gases (typically liquid nitrogen) as a coolant, replacing conventional cutting fluids.
Application: Especially effective in machining heat-resistant materials such as titanium alloys, Inconel, and hardened steels.
Advantages: Extends tool life by 2–5x, eliminates thermal distortion, and enhances environmental sustainability by removing chemical coolants.
Enterprise Impact: Reduces cost per part in industries like aerospace and medical devices where high-value materials are common.
Modern tool coatings like Titanium Aluminum Nitride (TiAlN), Diamond-Like Carbon (DLC), and nano-structured multilayers drastically improve performance.
Functionality: Coatings improve hardness, reduce friction, and allow tools to withstand high temperatures without breakdown.
Advantages: Enhanced wear resistance, improved chip flow, and better cutting at elevated speeds.
Enterprise Impact: Reduces frequency of tool changeovers, boosts productivity, and cuts down on scrap rates from heat deformation.
These tools combine milling, drilling, and turning functions into a single unit or machine setup.
Application: Used in advanced CNC systems (e.g., mill-turn machines) for complex geometries in a single setup.
Advantages: Minimizes part handling, reduces errors from fixture changes, and compresses lead time.
Enterprise Impact: Perfect for short-run production or high-mix/low-volume environments where flexibility and throughput are critical.
Some enterprises now use tooling that works in tandem with 3D printing and post-machining stages.
Application: Common in aerospace and medical, where near-net-shape parts are printed and then refined with precision tools.
Advantages: Maximizes material usage, enables custom internal geometries, and ensures final tolerances.
Enterprise Impact: Supports lightweighting initiatives, design innovation, and faster product iteration cycles.
Sensor-integrated tools can monitor cutting forces, vibration, temperature, and wear in real time.
Application: Can be used across CNC platforms and in Industry 4.0-enabled environments.
Advantages: Enables predictive maintenance, alerts operators to tool degradation, and enhances machine learning models.
Enterprise Impact: Reduces unplanned downtime, improves part quality consistency, and integrates tooling data into the broader digital thread.
These systems allow tools to be swapped or reconfigured without removing the entire setup.
Application: Valuable in multi-product lines or high-variety manufacturing.
Advantages: Reduces setup time, minimizes calibration errors, and allows for faster shift changes.
Enterprise Impact: Increases machine uptime and shortens response time for custom orders or design changes.
Evaluate existing tooling systems and identify inefficiencies—whether in tool change frequency, scrap rates, or dimensional variance. Align tooling upgrades with specific production challenges.
Work closely with manufacturers and technical reps to choose the right tool for the job. Many suppliers offer custom tooling solutions, digital integration services, and process optimization workshops.
Modern tools with embedded sensors can link to CNC systems, MES platforms, and digital twins. This integration allows for real-time performance monitoring, adaptive machining, and smarter scheduling.
Invest in upskilling teams. Ensure CNC programmers understand the tooling parameters, while operators are trained in proper handling, maintenance, and diagnostics of advanced tools.
Begin with a pilot line or a high-cost production area. Track KPIs like tool cost per part, surface finish, or downtime. Use this data to build business cases for broader implementation.
Enterprises that view tooling as a core operational asset—rather than a consumable—stand to gain competitive advantages in cost, quality, and responsiveness. By leveraging cutting-edge techniques and integrating them into a smart, skills-based manufacturing culture, companies can transform their production capabilities from the ground up. In an era where precision, efficiency, and agility define market leadership, tooling innovation is not optional—it’s essential.